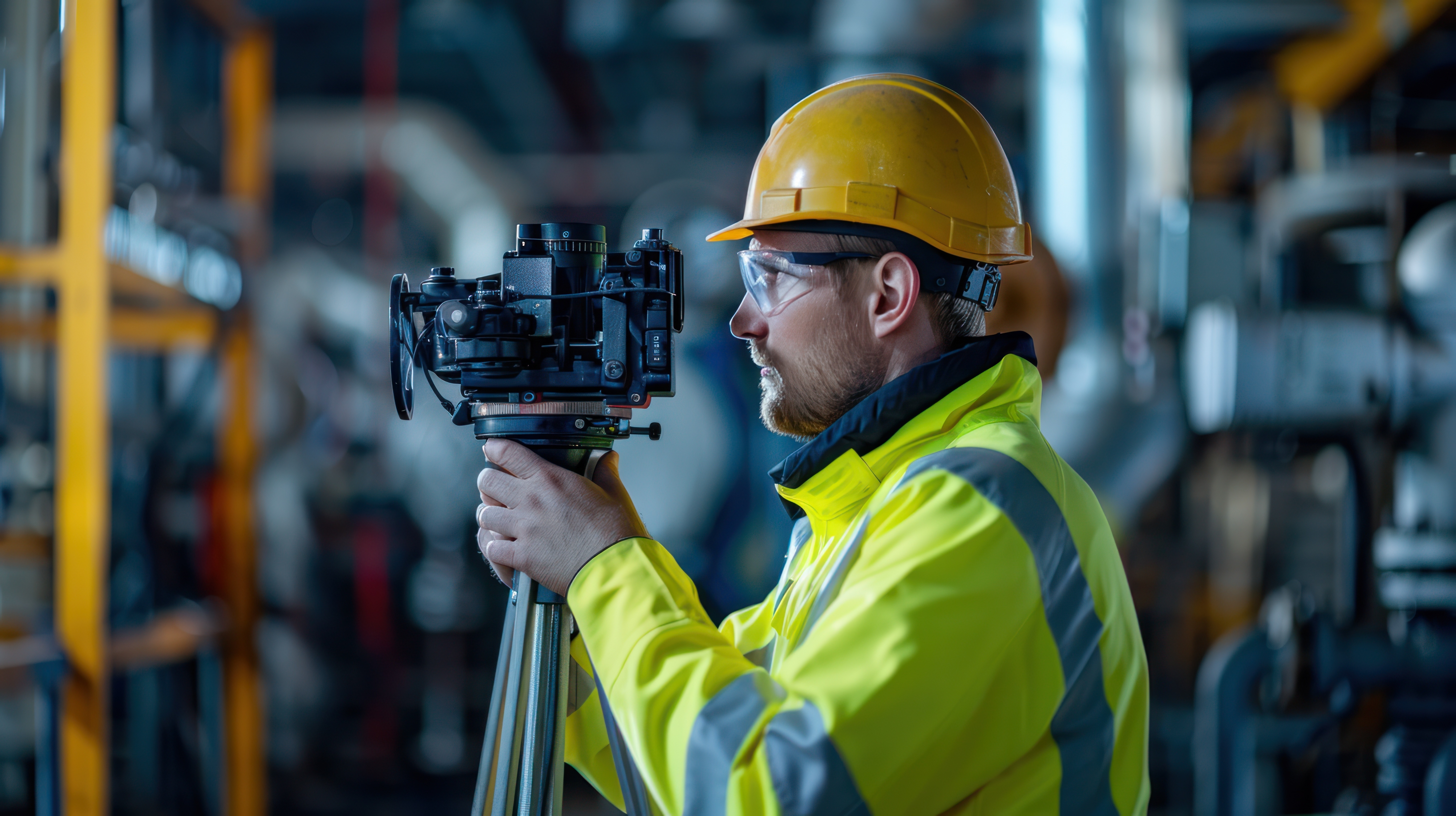
Laser Scanning of Buildings
Laser scanning technology has become a game-changer across a wide variety of industries, from construction and architecture to manufacturing and archaeology. By capturing highly accurate, three-dimensional representations of objects and environments, laser scanning enables professionals to visualize and analyze real-world data in ways that were once impossible.
What is Laser Scanning?
Laser scanning, also known as LiDAR (Light Detection and Ranging), is a non-contact measurement technology that uses laser beams to capture the geometry of objects or environments.
The basic principle behind laser scanning is simple: A laser scanner emits rapid pulses of light toward the surface being scanned, and then measures the time it takes for each pulse to reflect back to the scanner. This information is used to calculate the distance between the scanner and the object, creating a precise, 3D point cloud of the scanned area.
A typical laser scan can capture millions of data points per second, and each of these points represents a specific coordinate in three-dimensional space. When combined, these points form a "point cloud," which is a digital representation of the scanned environment. The more data points captured, the higher the resolution and accuracy of the model, enabling detailed analysis and visualization.
How does Laser Scanning work?
1. Laser Emission: The laser scanner sends out pulses of light. These light pulses travel until they hit a surface, like a building wall or the ground.
2. Return Signal: The scanner measures the time it takes for the light pulse to return after hitting the surface. This is known as the "time of flight."
3. Distance Calculation: Based on the time of flight, the scanner calculates the distance from the scanner to the surface. The result is a precise measurement of that particular point’s position in space.
4. Point Cloud Creation: As the scanner moves or rotates, it continues to emit laser pulses, capturing millions of data points from different angles. All of these points are then combined into a 3D point cloud, which serves as the digital model of the environment.
5. Data Processing: After the scan is complete, the point cloud data is processed using specialized software to generate detailed 3D models or to integrate the data into other applications like digital twin platforms for further analysis.
Types of Laser Scanning
-
This method uses a stationary scanner placed on the ground, typically at specific locations around a site. It is ideal for capturing large outdoor environments like buildings, construction sites, and infrastructure.
-
In this method, laser scanners are mounted on vehicles or drones, allowing for rapid data capture of large areas, such as roads, highways, or urban landscapes.
-
This technique uses sensors mounted on aircraft or drones to scan large, remote, or difficult-to-reach areas, such as forests or entire cities. It is especially useful in topographic surveys and mapping.
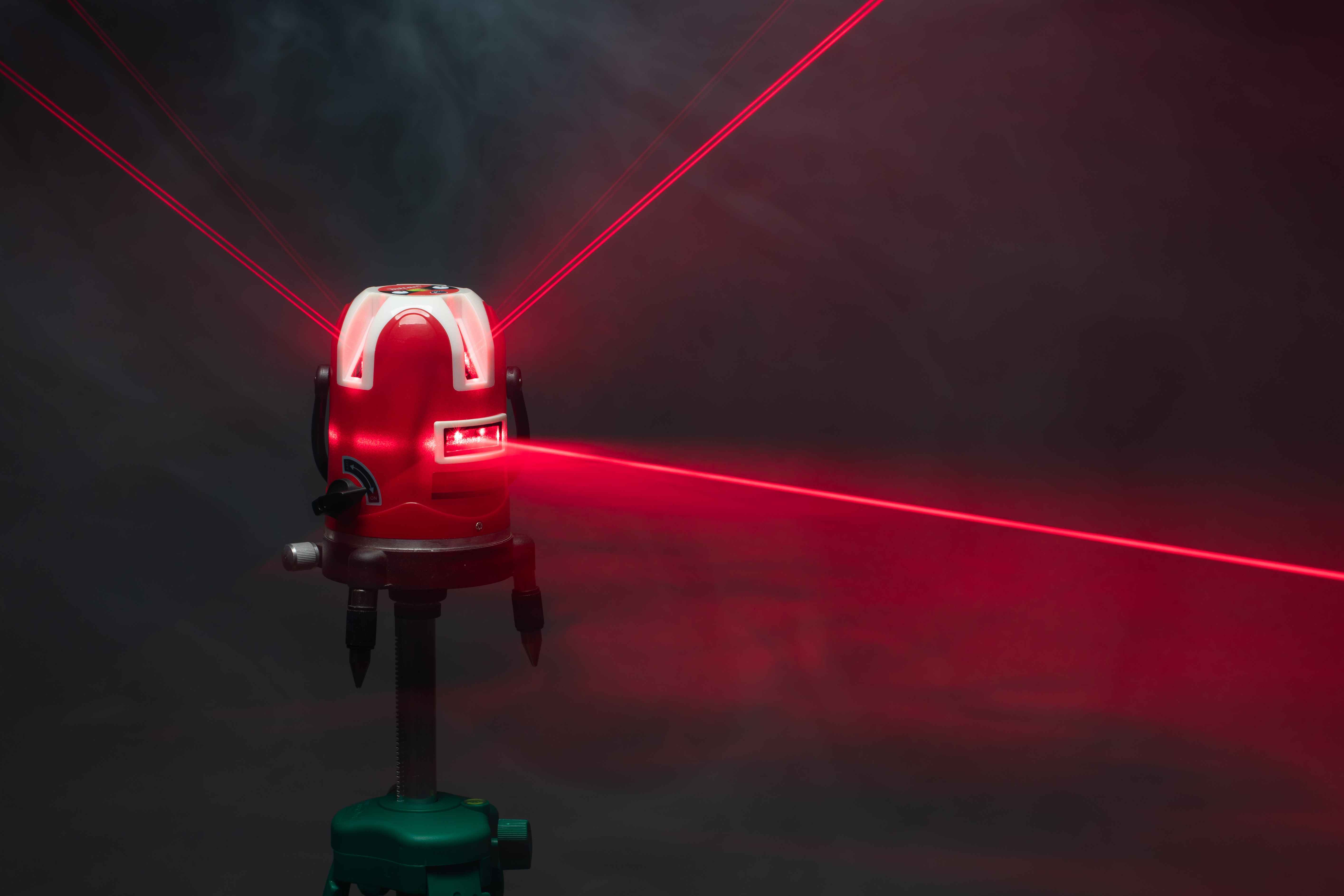
Benefits of Laser Scanning
-
One of the primary reasons for using laser scanning is its ability to capture data with exceptional accuracy. Laser scanners can measure distances down to millimeters, ensuring that the 3D models created from the point cloud are highly precise. This level of accuracy is invaluable in applications like architectural design, engineering, and construction, where small errors can lead to significant issues or costly delays.
-
Traditional surveying methods can be slow and labor-intensive, often requiring teams of workers to take individual measurements manually. Laser scanning dramatically reduces this time commitment. A single scan can capture vast amounts of data in a matter of minutes, allowing professionals to cover large areas quickly and efficiently. This speed is particularly beneficial for complex projects with tight deadlines.
-
Unlike traditional methods, laser scanning captures every detail, no matter how small, and in 360 degrees. This includes hard-to-reach areas, complex geometries, and hidden spaces that might be overlooked in manual measurements. For example, in the construction industry, laser scanning can capture the entire structure of a building, including interior features and structural elements, all in one pass.
-
Laser scanning is a non-contact method, meaning there is no need for physical contact with the environment being scanned. This minimizes the risk of damaging sensitive structures or creating safety hazards on the job site. It’s also safer for workers, as they don’t need to access dangerous or difficult-to-reach areas to take measurements.
-
Once the data is processed into a point cloud or 3D model, it can be visualized in various software applications, making it easier for stakeholders to understand the project’s scope and design. 3D models can be rotated, zoomed in on, and analyzed in ways that 2D drawings or photographs cannot. This improved visualization aids in decision-making, reduces misunderstandings, and fosters better collaboration among team members.
-
Laser scanning provides a digital "snapshot" of a project at any given point in time. These detailed, accurate records can be used for future reference, maintenance, or renovation. For example, in the case of historical preservation, a laser scan can create a permanent, detailed archive of a monument or building before any restoration work begins.
-
While laser scanning technology may have an initial investment cost, it often results in cost savings over the course of a project. The efficiency of the process reduces labor costs, while the accuracy of the data reduces the risk of costly errors and rework. Additionally, laser scanning can be used to generate more accurate cost estimates, helping avoid budget overruns.
-
Laser scan data can be seamlessly integrated into other software applications, such as CAD (Computer-Aided Design), BIM (Building Information Modeling), and GIS (Geographic Information Systems) and digital twin platforms. This compatibility enhances workflows, improves the accuracy of project models, and ensures that data is consistent and up to date across all platforms.
How dTwin uses Laser Scanning
dTwin uses point clouds from laser scanning to build the visualization of the built asset. The point clouds can be the sole basis for visualization or can be combined with BIM models or 3D photogrammetry. BIM elements can also be derived from the point clouds. The different types of visualization can be overlayed and compared.
IoT sensors can be linked to the visualization resulting from laser scanning. This allows real-time data to be localized and visualized via heatmaps. But many other data such as photos, videos, descriptions or technical specifications can also be linked to the point clouds.
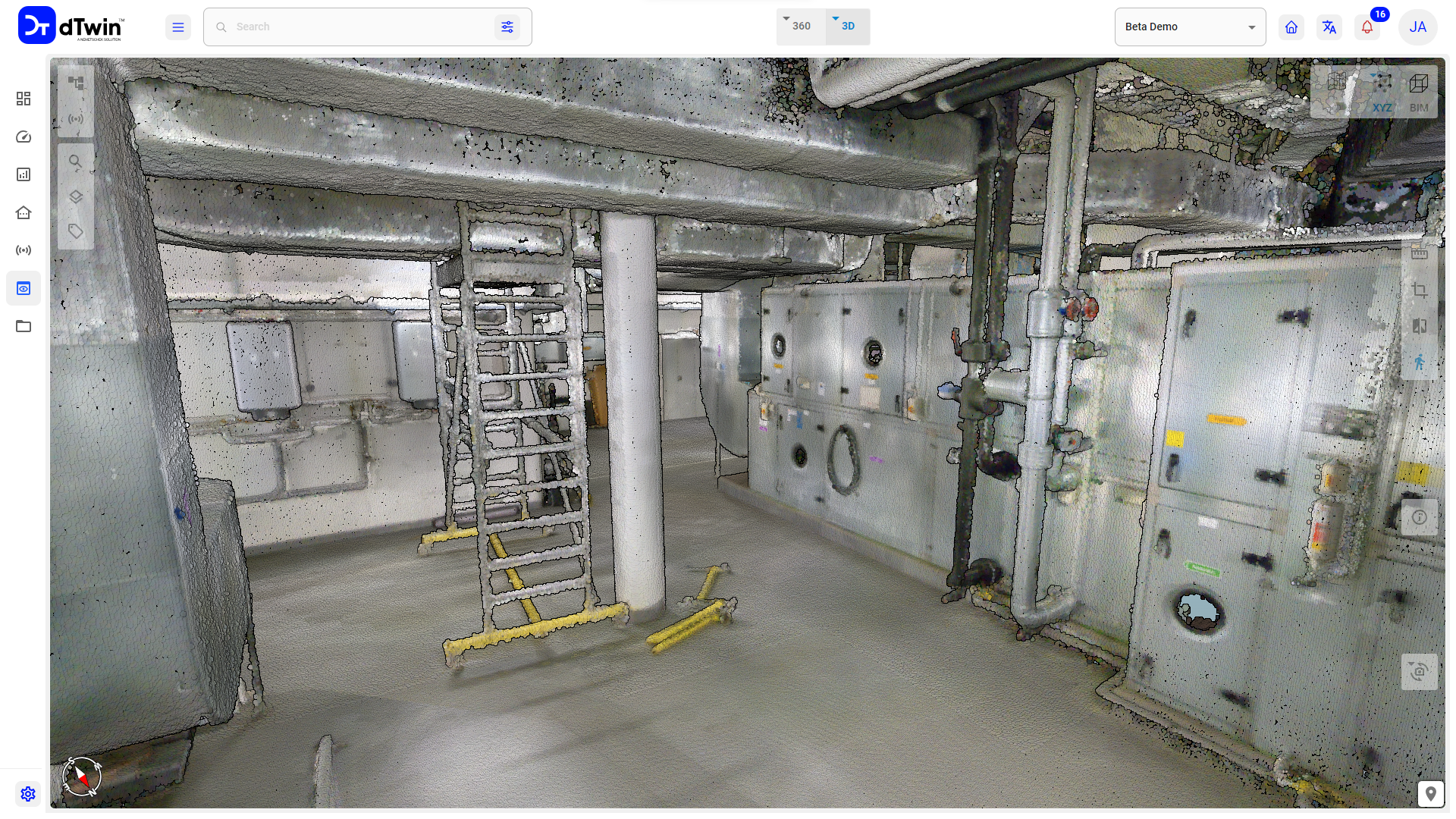